
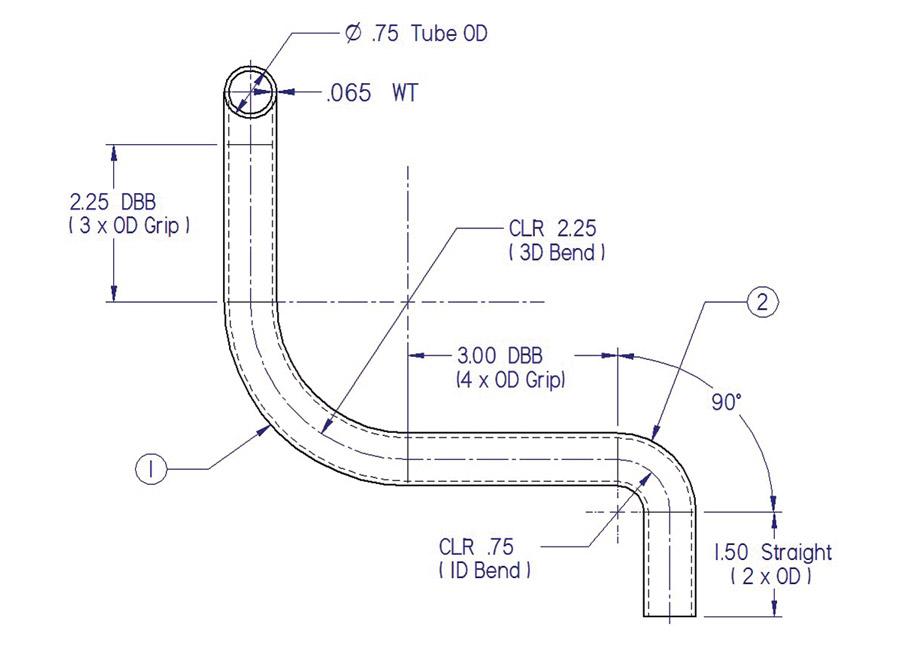
Now we just add the bend offset (5 7/8″ in the table from bending 101), and put a line 5 7/8″ from one of the lines that you drew to mark the end of the bend. So draw 2 more lines, each 3.12″ from the centerline. Lets say you have a tube that is 45 inches long, and you want a 60 degree bend (done on a 1.75×6 CLR die) right in the middle of it. Now that you know how to calculate the length of a bend, and where a bend will start based on where you clamp it in the machine, you can easily put a bend in the middle of a piece of tubing. Now you can add the bend length to your straight tube lengths and know your actual total cut length for your tubing! So if you’re bending 90 degrees on a 6″ CLR die, your tubing in the bend is 90 *. Just multiply the degrees you’re bending by the numbers below and you will get the length of tube in the bend. How Much Tubing is in a Bend?Ĭalculating the tubing in a bend is very simple. In bending 102, you will learn how to calculate the length of tubing in a bend, and also how to put a bend in the middle of a length of tube. Now you can overbend every 90 on that material by 3.5 degrees and they will all be spot-on! Springback is different for every material. So you bend to 90, snug the machine up, read 86.5, then bend to 93.5 and pull out the tube and you will be at EXACTLY 90 after springback. Read your degrees, we’ll say for example that you read the degrees at 86.5. Tighten the valve, and hand pump the ram until it is just barely tight on the material. If you want to bend a 90, bend EXACTLY 90, and then release ram pressure until the material is loose in the machine.
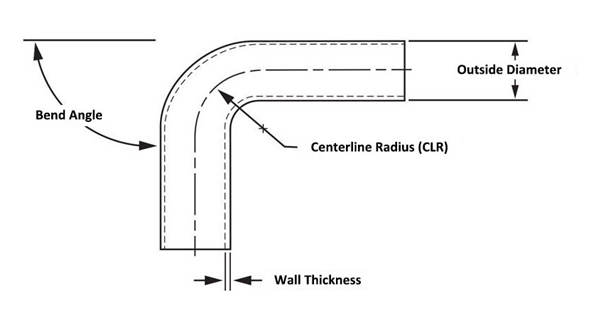
Here is the best way to measure your springback- Put straight material in the machine and hand pump the ram until it is just barely tight but not bending yet. If you don’t like bend offsets (like if you’re used to another machine), just buy one of our bend location gauges (click HERE – new window), it allows you to tape measure from bend start to any place on the tubing you want. Putting bends where you want them accurately is the foundation of accurate tube work. The bend will start at exactly 10 inches from the end of the tube. This line you just drew is where you line up the tube with the clamp block in the machine (“MARK TUBE HERE” in above image). Now draw a line that is 5 1/4″ closer to the end of the tube from your first line (5 1/4 is the bend offset from the table below). If you want to make a bend on a 4.5 radius die, and you want that bend to be 10 inches from the end of a piece of tube, mark a line on the tube 10 inches from the end. The bend offset is the distance between the start of the bend and where you line up the tube in the machine. The Rogue Fabrication bender has a fixed bend offset for every radius of die. In bending 101, you will learn how to put a bend where you want it, based on where the bend starts, and how to bend the right amount. Bending Tube with a Rogue Model 600 Bender, 101: The basics
